Leveraging remote collaboration to augment existing inspection protocols.
The pharmaceutical manufacturing industry is incredibly important to healthcare around the world. With growing pressure to produce affordable medication for growing patient populations in developed and developing nations alike, regulatory authorities must ensure that manufacturers deliver high-quality products while maintaining transparency across their entire lifecycle. Traditionally, this is achieved through both internal and external audits and inspections.
A more integrated future is now more accessible than ever before. Recently, the Parenteral Drug Association hosted a workshop, where experts discussed the impact of COVID and the impact remote audits can and will have on the industry. Leaders from these diverse fields spoke about how new approaches are transforming today’s inspection processes with emerging technologies.
The pharmaceutical industry must ensure safety, quality and compliance across their supply chain. However, with an uncertain FDA roadmap thanks to COVID-19 as well as restrictions conducting their own internal audits; companies have been left in a difficult position.
With new guidance and technology available, companies are equipped with a strategic foundation for their future inspection protocols. This will help them reduce surprises during inspections by implementing an integrated hybrid protocol capable of conducting both in person and remote inspections – all while maintaining compliance standards.
Step 1: Use a Risk-Based Model to Determine Which Audits and Inspections can be Conducted via Remote Collaboration
Each company has their own inspection protocols and processes. However, this does not mean that a physical audit is required in every case.
For example, inspections can be conducted remotely under some of the following conditions: 1) initial qualification; 2) ongoing compliance; 3) qualifications for re-approval; 4) verification of corrective actions.
Compliance experts suggest a risk-based approach to determining which visits should be conducted in person. The risk-based model is unique to each company and often differs on a variety of factors such as:
- Is the supplier new or existing?
- Is there a history of compliance issues?
If there is a serious concern or a new supplier, an in-person visit is best. However, for other routine conditions, remote audits are not only suitable, but actually a more beneficial option.
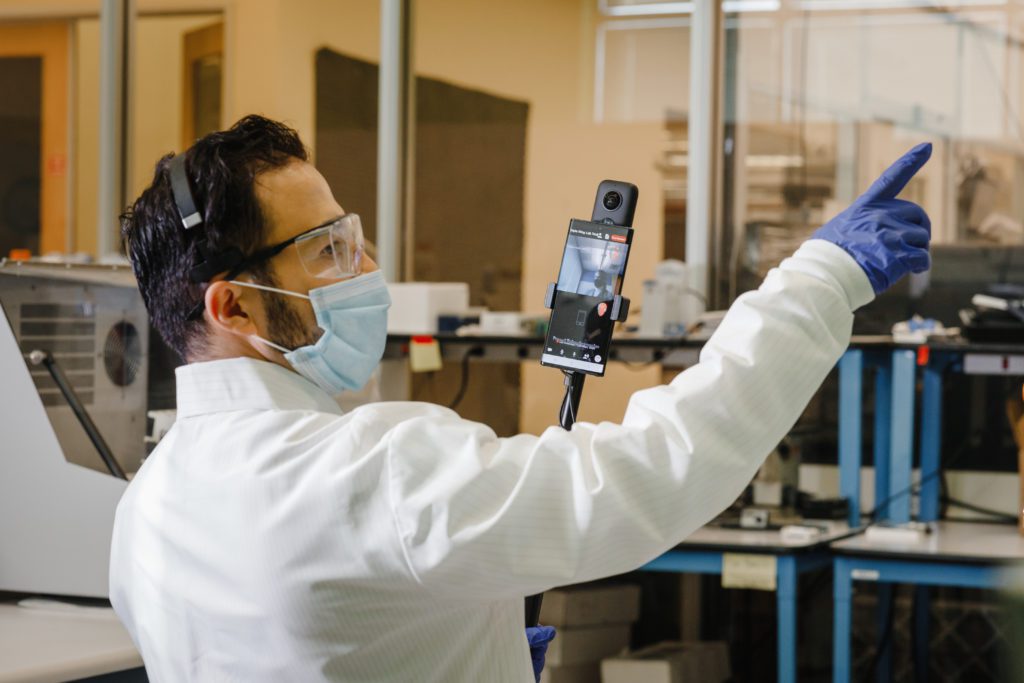
Step 2: Choose the Right Tools for the Right Job
During COVID, many companies leveraged standard videoconferencing platforms out of necessity. However, these platforms were not designed for site shared context. Using standard video platforms only allows visitors to see from one point of view, indicated by the host.
Due to rapid innovation over the past few years, there are a variety of tools available, purpose-built to serve a variety of needs. Click here to learn more about technology built for purpose.
For remote audits and inspections, technology should support a similar experience as being in person. There are several factors to consider in a platform, such as:
- 360° Capabilities: 360° remote collaboration provides viewer autonomy, allowing each visitor to control their point of view.
- Connectivity Options: large pharmaceutical factories often struggle with reliable connectivity throughout the site. Therefore, platforms that work on WiFi or local LTE/5G networks.
- Real-time Capabilities: in order to maintain transparency and confidence, pre-recorded or lagging sessions will not work as a substitute for in-person inspections.
- Collaboration features: document sharing and annotation can help auditors and stakeholders review files, documents, and checklists in real time.
Step 3: Prepare
Virtual audits and inspections are not necessarily more difficult with the right preparation.
There are several steps to consider when preparing for a remote visit. When followed, these steps ensure the transparency and collaboration needed to execute successfully. Steps for success
- Identify a remote protocol: this should be separate from your existing protocol, but take into account opportunities and limitations in the remote space.
- Be clear on SOPs: it’s important to share SOPs and protocols ahead of time to make sure visitors and groups are on the same page well in advance.
- Test connectivity: ensure the site has proper bandwidth and connectivity before hosting a virtual visit. Understand if your team will be using site WiFi or LTE/5G network coverage.
- Conduct a test run: establish who will be present during the audit. Be sure everybody understands their roles and how to operate the remote technology.
- Set a schedule: communicate a clear schedule ahead of time. Review the schedule once more when all parties are present.
Conducting a virtual inspection? Click here for a comprehensive checklist.
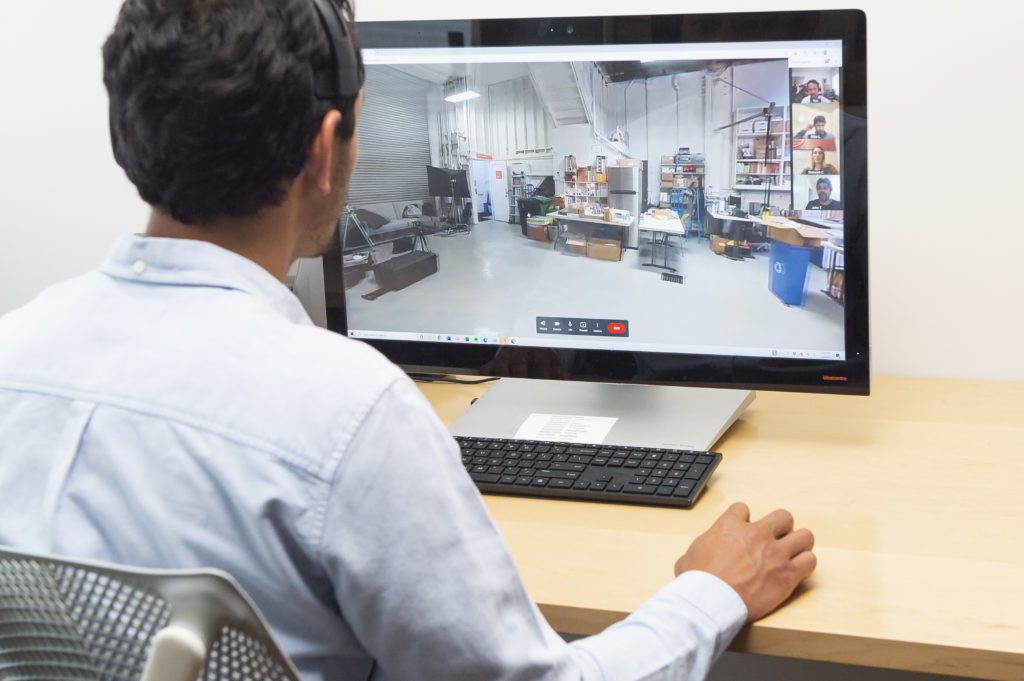
In Conclusion
The main benefit of a hybrid strategy is the significant cost and time saving potential due to less travel.
Remote inspections also help companies avoid distance restrictions, such pandemic lockdowns and visa issues.
A hybrid inspection model helps companies maintain continuous quality management. This ensures any issues or compliance threats are addressed swiftly.
Hybrid collaboration is not only possible, it’s powerful. With the ability to be on site without sacrificing quality, companies are in a strategic position to minimize travel cost and carbon emissions while reimagining their operations.
About Avatour
Avatour is the remote collaboration platform for site meetings. We’re committed to creating a future beyond distance. To learn more about what our platform can offer your business, click here to book a demo.